Altenburger Maschinen Jäckering
Innovative milling and drying-pulverising technology.
Powerful machines are essential in the production of many types of product. The production equipment has to meet different requirements, however, depending on the type of application.
We have been developing and manufacturing milling plants and dryer-pulveriser systems in-house since 1955, centred around our ULTRA-ROTOR air turbulence technology. These systems enjoy great popularity thanks to their user-friendliness, flexibility and cost-effectiveness.
You can find our most recent leaflet here.
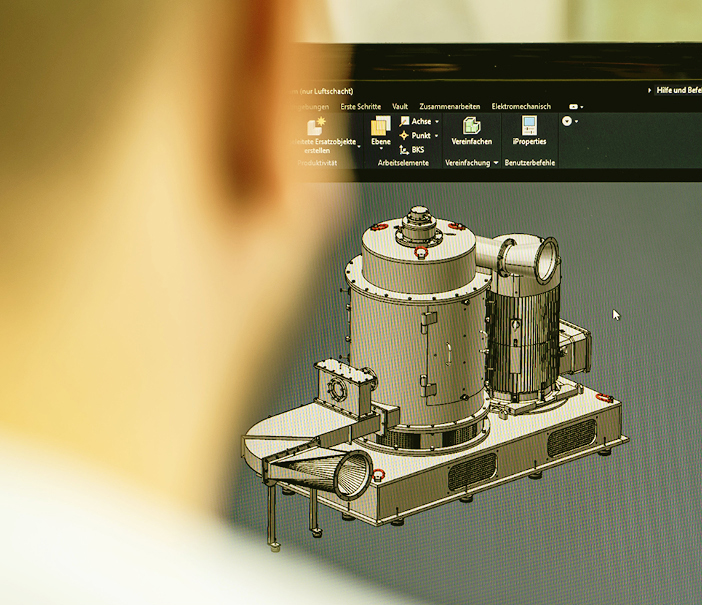
We develop solutions to promote your success
Efficient milling and dryer-pulveriser systems for specific applications and processes.
Tailored to your requirements and well thought through, right down to the last detail. This means that you receive highly specialised solutions, unique on the market, for your specific applications. Pioneering and always state-of-the-art, to guarantee your long-term success. This makes us your ideal partner for milling and dryer-pulveriser systems for the production of various products made from main product and by-product streams.
How the ULTRA-ROTORS work
Our ULTRA-ROTOR uses air turbulence milling technology. Its history goes back as far as the mid 1950s. It is an innovative system that employs efficient machinery and processing equipment, installed in a robust steel support structure. And we are continuously working to further improve its design. As well as pulverising, our ULTRA-ROTOR allows milling and drying processes to take place in a single work step. The system is powerful, highly versatile and extremely cost-effective to operate.
The basic principle
Inside the machine, a high-performance rotor rotates at high speed. At the same time, a downstream fan ensures a high through-put of air. This, in connection with the special design of the inner milling chambers, creates extreme air turbulence. This turbulence is the basis for the milling process in the ULTRA-ROTOR.
Pulverising
During the milling process, the turbulent air directs the particles in such a way that they collide with each other again and again. This causes them to break at their natural breaking points. Mostly, it is the mass of the particles themselves that provides the necessary breaking force. Compared to other pulverising systems, our ULTRA-ROTOR mills the product in a particularly gentle fashion. The milling heat that is generated is discharged very effectively via the large volumes of air used in the milling process.
The coarseness can be adjusted, even down to the micron range. After the milling process, the milled product can be separated via downstream sieves or sifters. If a pressure-resistant design is selected, even explosive products can be milled in our ULTRA-ROTOR. And even cryogenic milling is possible, if required.
The pulverising work of the ULTRA-ROTOR is based essentially on air turbulence generated by the rapid rotary motion of the rotor combined with a high through-put of air.
The rotor consists of a solid main shaft to which up to seven centrifugal plates are attached. This is driven by an electric motor via a V-belt connection. Peripheral speeds of up to 130 m/s can be achieved, depending on the design of the motor and the machine.
The air through-put is generated by a downstream fan. The air which the fan draws in from the atmosphere makes the system operate at a slight negative pressure.
Vertically aligned milling tools/milling plates are attached at regular distances around the outer edge of each centrifugal plate. Air turbulence is generated in the intermediate spaces by the rotary motion and air through-put. If the product gets caught up in the air turbulence, the particles change their speed and the direction of their flight path within a very short time. This leads to undefined impact processes, which cause the particles to collide with each other and result in the breakdown of the particles. Only a small part of the pulverising process is caused by collision between the particles and the stationary or rotating parts of the machine. The product typically spends only a fraction of a second in the ULTRA-ROTOR.
On reaching the downstream filter, the air and product stream are once again separated from each other.
Depending on the system settings, this operating principle enables a wide variety of products to be finely ground to differing degrees of fineness. Even though the grinding process releases a corresponding amount of frictional energy, the resulting temperature can usually be dissipated efficiently by the air through-put.
If the product to be processed is extremely sensitive to high temperatures, our ULTRA-ROTOR technology also offers the option of cryogenic processing.
In addition, we are able to separate the pulverised particles through the use of downstream sieving technology.
Processing explosive raw materials is already a proven and certified procedure on the basis of constructive explosion protection. This can take the form of plant and equipment designed to be pressure shock resistant or pressure-relieved or, in extreme cases, by the use of inerting.
Drying-pulverising
In drying-pulverising systems, damp products or suspensions are milled and dried in one work step. This is achieved by passing the process air through an upstream heating unit before the air enters the ULTRA- ROTOR. The thermal impairment of the milled product is minimal for two reasons: Firstly, the product is only in the machine for a few fractions of second and, secondly, evaporative cooling takes place as the water evaporates. This means that our dryer-pulveriser system is also suitable for processing temperature-sensitive products.
Another field of application of the ULTRA-ROTOR is referred to as the drying-pulverising process. This involves simultaneously pulverising and drying moist products or suspensions which are introduced into the ULTRA-ROTOR using either a screw feeder or even a pump.
The drying-pulverising process is largely identical to the milling process. The only difference lies in the simultaneous supply of hot air as a carrier gas. The combined action of the hot air and the turbulent air flow enables the air to rapidly absorb and evaporate the moisture adhering to the product particles.
The resulting cooling due to evaporation and the short dwell time makes for a very gentle drying process and even allows us to efficiently process temperature-sensitive products such as proteins.
Depending on the application, the intake temperature of the hot air can be up to 400° Celsius.
Coating
Coating involves coating/covering the surface of the product particles in order to improve their flow properties, for example. Solid or liquid additives, such as stearate or stearic acid, are added to the product during milling in the ULTRA-ROTOR. During the milling process, each particle of the product is then entirely and uniformly covered by the coating material. The coating process can also take place in the course of a drying-pulverising process.
The term coating refers to the surface coating of product particles. This method of treatment is used, for example, to improve a product’s flowability.
During coating, treatment agents such as stearate or stearic acid can be added to the ULTRA-ROTOR milling chamber. During the milling process, the simultaneous action of breaking down the particle structure and the effect of the air turbulence causes each product particle to be enclosed by the treatment agent. This results in a very uniform surface coating. The combination of a simultaneous drying-pulverising process is also a possible option.
ULTRA-ROTOR with sifter
The CS version of the ULTRA-ROTOR has a separately driven sifter. This makes it possible to separate out any large particles and return them to the milling process. The particle size distribution can thus be more precisely delimited.
A variant of the ULTRA-ROTOR model that deserves special mention is the so-called CS machine.
This is an ULTRA-ROTOR with a separately driven sifter wheel integrated in the top area of the ULTRA-ROTOR.
Due to the variable adjustable speed of the sifter zone, large particles are separated out and returned to the lower milling area of the ULTRA-ROTOR to undergo a renewed milling process.
This method makes it possible to set a very narrow particle size distribution, which reduces undesirable oversize particles to a minimum.
Product Overview
We offer our customers high-precision machines for customised process solutions. This is why we produce our sophisticated ULTRA-ROTOR solutions as tailored, one-off systems. During product development, we take empirical test data and the individual requirements of our customers into account in equal measure.
The following table shows a selection of the various basic versions and available size increments. Special designs are available on request.
Size | Dimensions | Typical output | Maximum drive output | Typical water evaporation |
ULTRA-ROTOR, Model I | 1400 x 1000 x 920 mm | 100 kg/h | 22 kW | 20 kg/h |
ULTRA-ROTOR, Model II | 1590 x 990 x 1480 mm | 200 kg/h | 45 kW | 100 kg/h |
ULTRA-ROTOR, Model III a | 2610 x 1360 x 1740 mm | 1.500 kg/h | 132 kW | 200 kg/h |
ULTRA-ROTOR, Model V | 3110 x 1610 x 2200 mm | 5.000 kg/h | 315 kW | 750 kg/h |
ULTRA-ROTOR, Model VI | 3650 x 2150 x 2300 mm | 10.000 kg/h | 630 kW | 1.500 kg/h |
ULTRA-ROTOR, Model VII | 4200 x 2360 x 3700 mm | 20.000 kg/h | 1.150 kW | 3.500 kg/h |
Areas of Application
Our ULTRA-ROTOR technology is used in a wide range of industries. Because it allows a high degree of customisation, it can reliably process very different types of product. Its range of applications is therefore vast. Here are a few examples:
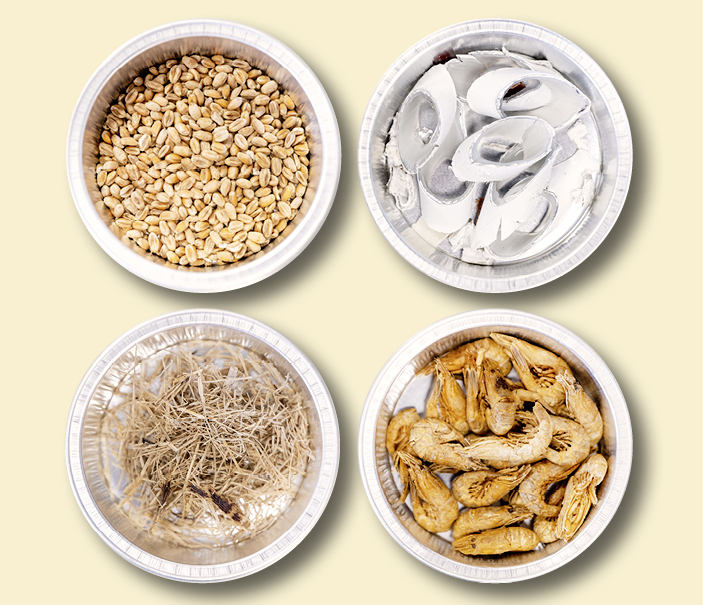
- Animal protein, from beef, pork, fish or insects
- Vegetable protein, from wheat, rice or algae, for example
- Vegetable pomace (solid remains after pressing), from carrot, beetroot, ginger or turmeric, for example
Rice, wheat, spelt, oats and wood
Calcium carbonate, aluminium hydroxide, clay
Aluminium, copper, magnesium, (electrical waste)
PVC
Methyl cellulose, anhydride
Do you need to process products that are not included in this list?
If so, then please get in touch. Together, we will find a suitable solution.
Test milling and test drying-pulverising
Your tests and trial series are carried out in the ULTRA-ROTOR Technical Centre
Would you like to know how well our highly specialised air turbulence mills can master your challenges? Whether these challenges involve pulverising, simultaneous drying/milling, coating, separating, cryogenic milling, inert processing, or other tasks: our experienced team will diligently perform the series of tests that you require. For these tests, we use your original grist. This allows us to determine the specific requirements of your application and take these into account in the design of your system.
Test milling or test drying-pulverising in two steps
To obtain the most meaningful and accurate test results for later use in practice, we set up our test rig, with regard to size, output etc., in line with the parameters dictated by your specific grist. As a rule, our team carries out the tests in two steps:
Step 1:
In a feasibility study, we check whether your grist can be processed to your satisfaction in our ULTRA-ROTOR. Depending on the moisture content of the test material, we will need around 25 to 50 kg of your material to implement this stage of the process.
Step 2:
In order to achieve optimal results, we recommend performing a second series of tests. These tests help us evaluate the specific long-term behaviour and further process parameters for your grist.
Here, we will need several hundred kilograms of your material. After each series of tests, we provide you with an extensive report. If you would like to observe these tests in person, we would be delighted. Then we will be able to discuss the results with you directly.
Development your products further in our Technical Centre
If you already use ULTRA-ROTOR systems, you can develop your products further in our Technical Centre. This keeps your own production line free for production, and you will also benefit from the experience of our specialists.
Experience the opportunities afforded by the ULTRA-ROTOR technology
Take advantage of the opportunities that our Technical Centre offers and experience first-hand the possibilities that the ULTRA-ROTOR technology opens up. Simply fill out our questionnaire so that we can prepare your trial series in the best possible way. Please attach any photographs or videos that may be relevant, and let us know when you would like your test series to take place.
The mobile ULTRA-ROTOR container system
Ideal for testing the ULTRA-ROTOR system at your premises, or for processing smaller quantities on a temporary basis.
Perhaps test milling in our Technical Centre is not feasible in your case, because your product needs to be milled while fresh? Or maybe you would like to process some smaller quantities without the risk of a large investment? Then rent one of our compact ULTRA-ROTOR dryer-pulveriser systems, which come in a 20' high cube container.
Each type of grist behaves differently. This often makes it necessary to carry out tests with the fresh original material in order to better assess its milling and drying behaviour and the properties of the milled product. To this end, we have mobile ULTRA-ROTOR systems that are available for you to use on a rental basis.
This system is installed in a 20' high cube container and includes an intake filter, hot air generator, dosing unit, cyclone, sieve, and switch cabinet. The equipment is made of stainless steel, to meet the most stringent hygiene requirements.
We have several ULTRA-ROTOR container systems available, so that we can rent out to more than one customer at a time. We would be happy to provide you with information on their availability.
Please contact us to find out more about rental conditions and availability.
Plant Planning
Comprehensive support from the planning stage through to commissioning
On request, we can assist you with all your planning and implementation steps, right through to the commissioning of your ULTRA-ROTOR system. Our experienced team will provide comprehensive support. This includes a goal-oriented consultation on site, a detailed 3-D plant design, recommendations regarding explosion protection, determination of the interfaces to any upstream and downstream processes, and much more. We would be delighted to provide you with more information about our services.
Service
Regular servicing will help to ensure that your ULTRA-ROTOR will still be working reliably many decades later. We have a well-trained team of experienced service technicians who look after our customers' equipment worldwide.
We also come to your assistance quickly and reliably if an emergency arises. You can reach us by telephone or email, as necessary.
Alternatively, you can fill out the following form. The information you provide will help us to identify any defects and to prepare possible solutions.